There are a few elements on the original chassis that are really not needed in a camper trailer. The big side walls, the rear ramp, the 2×8 pressure treated slats, are for mods and parts to hack back into the new design.
Cutting and welding the square tubing was fairly easy. Those areas receiving the heat from the gun are sanded down and cleaned from the powder coating layer that covers every inch of the frame. To avoid oxidation I’m using a little bit of phosphoric acid that bites into the metal and leave no trace. In some cases I’m immediately spraying some Steel-it. This last one is weldable, allowing for reparations and additional detailing.
Most of the ends of the square tubing frame are open, so a fair amount of work is focused on closing them or prep them to fit another piece. Eventually all the open ends will be welded and closed or capped with plastic lids to avoid excessive exposure to the elements, residual moisture trapping or simply to avoid the frame to collect debris from the road.
To be able to square up all the welds strong angled magnets and clamps are used especially because of tight spaces and under-the-carriage welds.
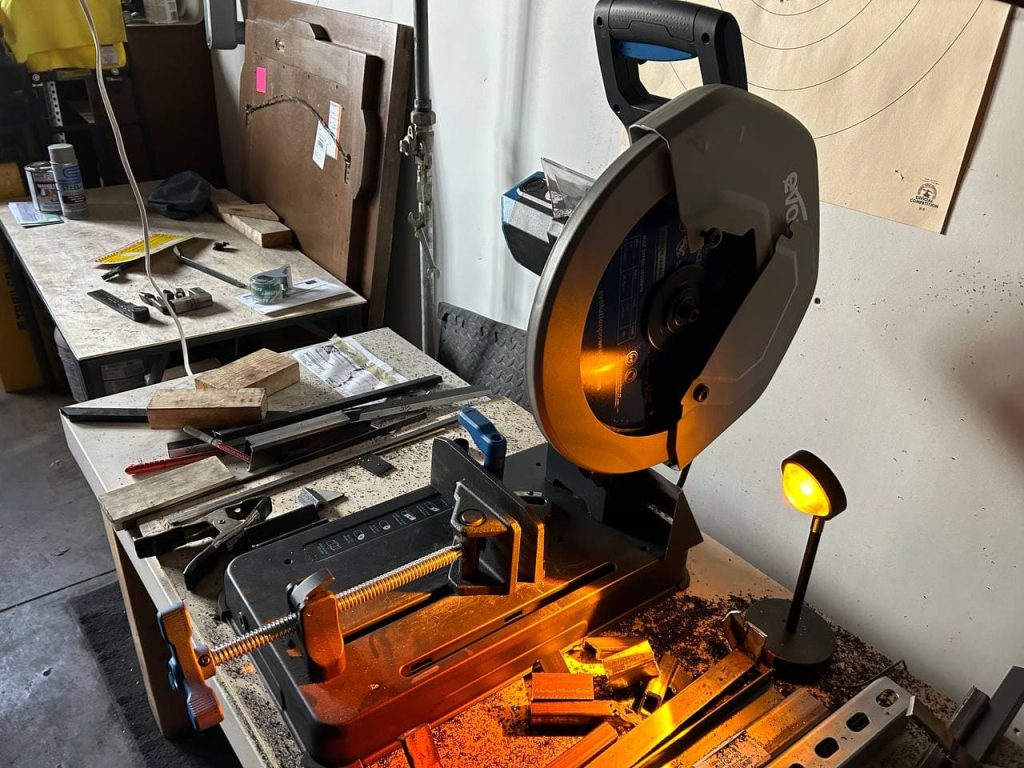
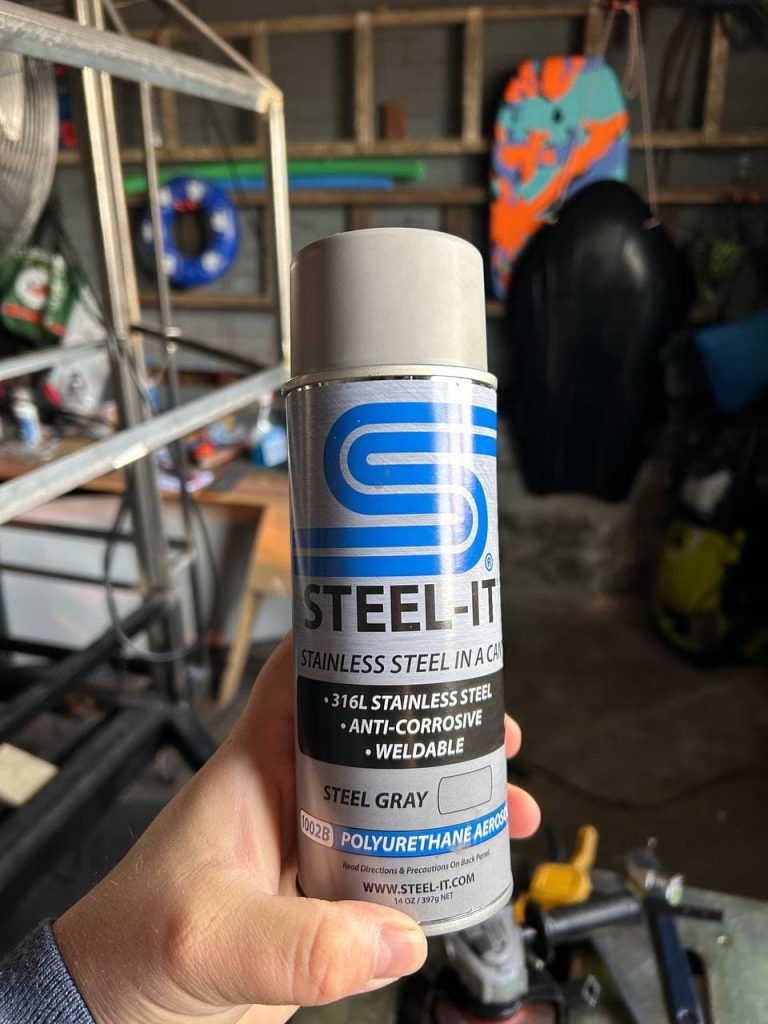
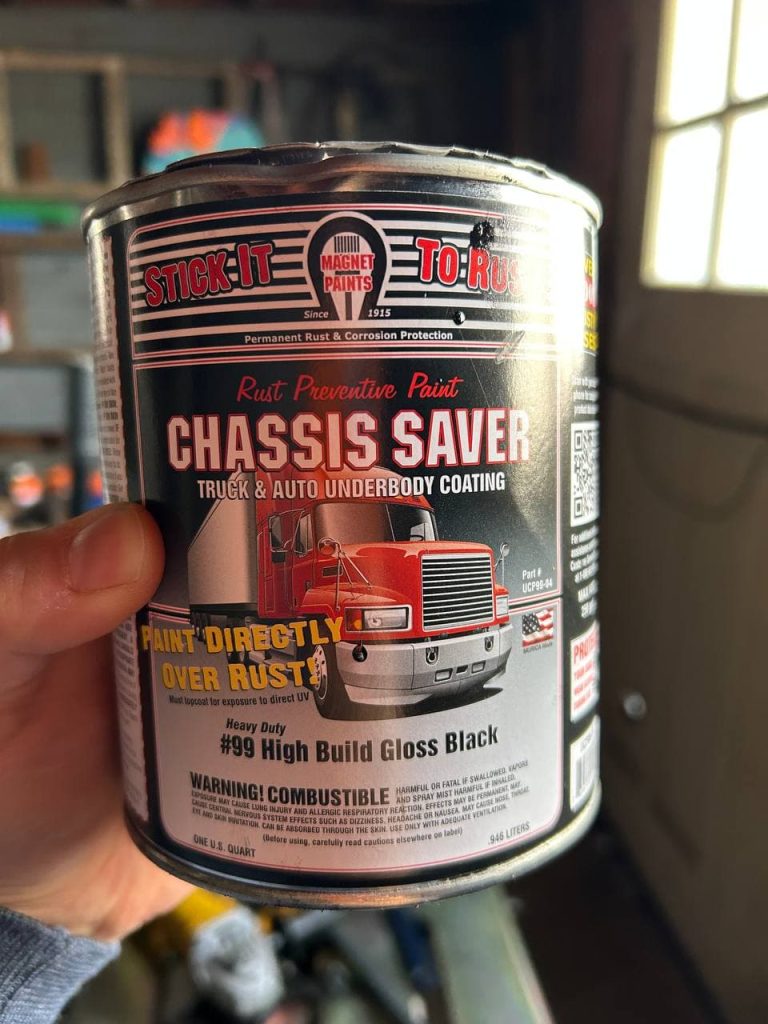
A few recommendations if you’re working on your project and start chopping on pieces of metal and welding:
- Use a fan or a vacuum system for dust and fumes. Both angle grinders and saws produce fine and medium size metal dust that goes everywhere, power outlets, drains and pipes, and most dangerously your eyes and nostrils. If possible, work outdoors.
- Wear any safety piece of gear possible, proper eyeware and guards. In addition, a good lightweight hat will save you from all these metal chips to find refuge in between your follicles.
- Wear welding friendly clothing. Natural denim is a great choice, and you can go as far as cotton socks and hats.
- Chose a pair of gloves that is tight and fairly insulated on the fingertips. handling metal means dealing with high temperatures, burrs, and high speed blades that can catch on loose pieces of clothing.
- Design a safe space around your focus area, thinking about cable management and travels from the tools and to the piece. Keep the area clean and free from water and store all chemicals away from the work area.
- Invest a small budget on the right tools and consumables for you. It’s a learning curve but It will save you headaches and ease your work exponentially, on the long run.
For some reason metal tools like grinders and blades have less safety aids than in the woodwork tools industry even if the hazards of working with hefty steel masses and chemicals are much bigger in a DIY setting.